For more than 70 years, Ray Products has built a reputation as a premier provider of pressure formed plastic parts. With a commitment to constantly upgrade our facilities with the highest quality equipment and latest technology, today we can manufacture custom plastic parts using our advanced, heavy-gauge pressure forming process, delivering the highest quality in the business while reducing tooling costs and turnaround times. With our experience, Ray Products will help guide what pressure forming is, the advantages of pressure forming, and what makes Ray Products a complete partner for your next project.
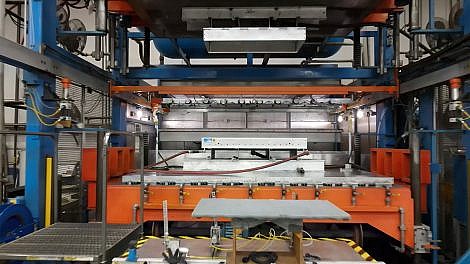
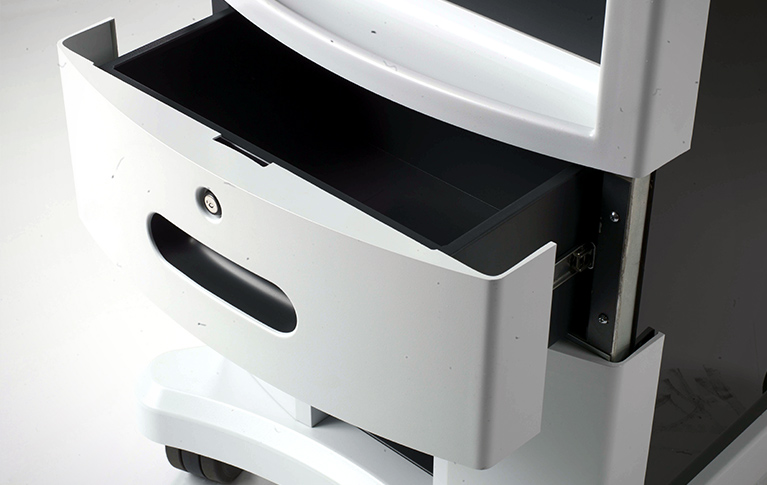
With the ability to combine multiple custom components into a single, seamless product, along with incredible cost-effective processing and the ability to replace fiberglass and steel, large part thermoforming opens up new vistas for manufacturing in volumes ranging from hundreds to thousands. No matter what the industry—transportation and mass transit, farming and agriculture, green energy, waste and water management, medical devices, or more—large part thermoforming can redefine what is possible for your business.
#1 – Large Part Thermoforming is Significantly More Cost-effective than Steel or Fiberglass Fabrication
The technology behind large part thermoforming has grown so efficient in recent years that many materials that once necessitated either fiberglass, steel, or a combination of multiple parts can now be streamlined into one cost-effective thermoformed plastic part. Let us pass on this savings to you. Large part thermoforming allows for tremendous efficiency as it transforms many high-dollar parts into one large, single, rigid and lightweight thermoformed plastic part.
#2 – You Have the Same Freedom of Material Choice with Large Part Thermoforming
Just as you might do with other smaller-scale thermoformed parts, large part thermoforming likewise allows you to choose the material type (any thermoplastic) color, thickness, and finish of your plastic material. Your project is only limited by your imagination, and a 10’ x 18’ forming area! The possibilities are essentially endless as you explore the same freedom of choice in large part thermoforming, particularly as the needs of your custom plastic project grow and become more complex. As your business grows, part-to-part repeatability will become more and more important, as well.
#3 – Large Part Thermoforming Yields Superior Molded Detail and Offers Seamless Part Repeatability
Large part thermoforming is synonymous with repeatability and superior molded detail, which is what your industry demands. You care about aesthetics, reliability and repeatability, which is why large part thermoforming could be ideal for your next project. When upgrading to large part thermoforming from fiberglass or steel, better aesthetics are often the natural result, largely because the material colors and finishes deliver a large seamless part.
We haven’t even mentioned the significance of light-weight options that large part thermoforming offers your business. Whether you need to thermoform 10-feet by 18-feet or smaller, large part thermoforming can transform the possibilities for custom parts manufacturing.
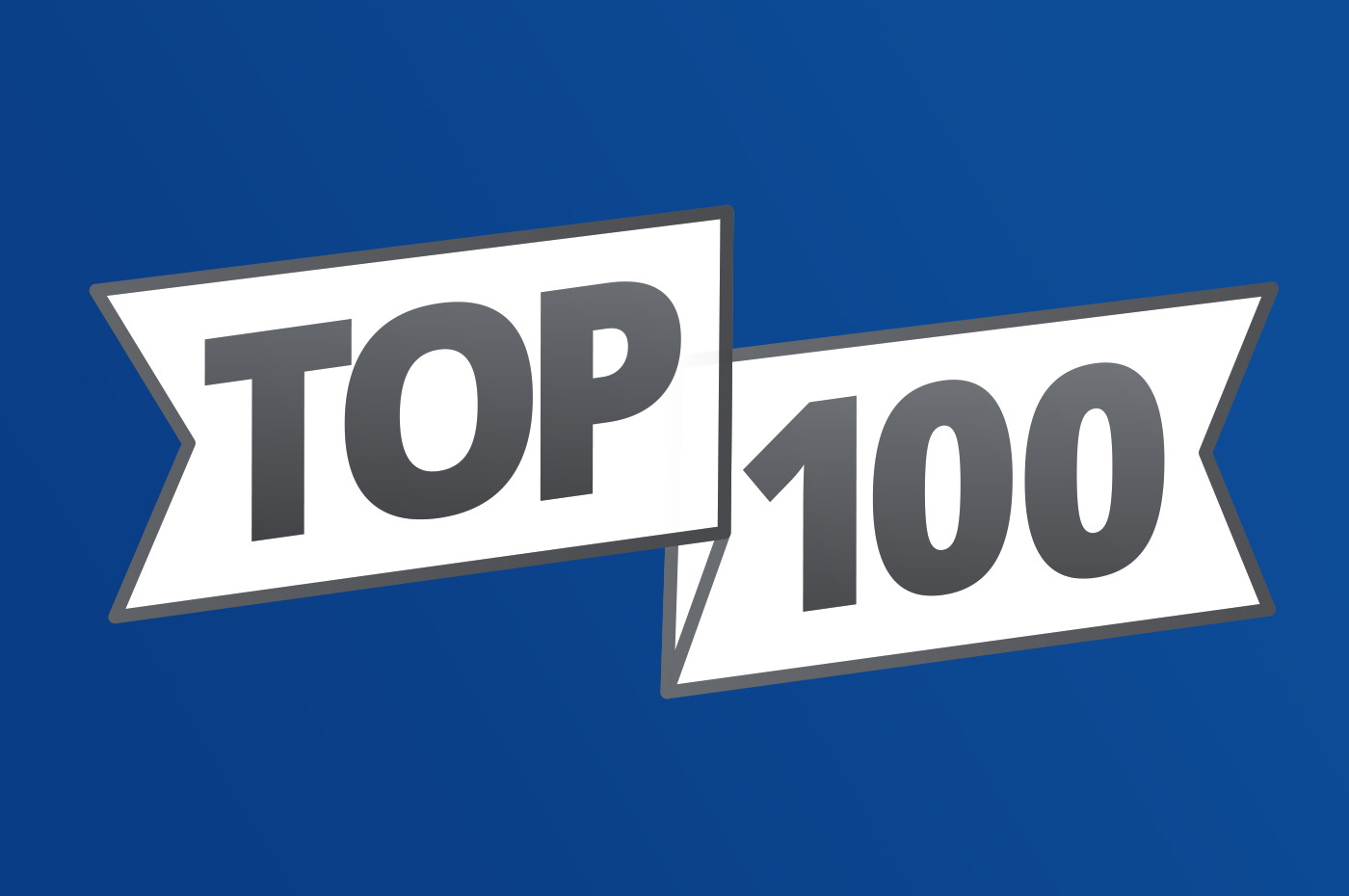
Every year, Plastics News conducts a survey of North American thermoformers and ranks them by annual sales. This year, for the first time, Ray Products made the top 100.
In fact, we received special recognition in the introduction to the report for moving “up 32 spaces”. That took us from 122nd last year to a respectable 90th this year.
Now, you may be thinking to yourself, “What’s the big deal?” Is celebrating 90th place really worth celebrating at all?
Yes, and here’s why:
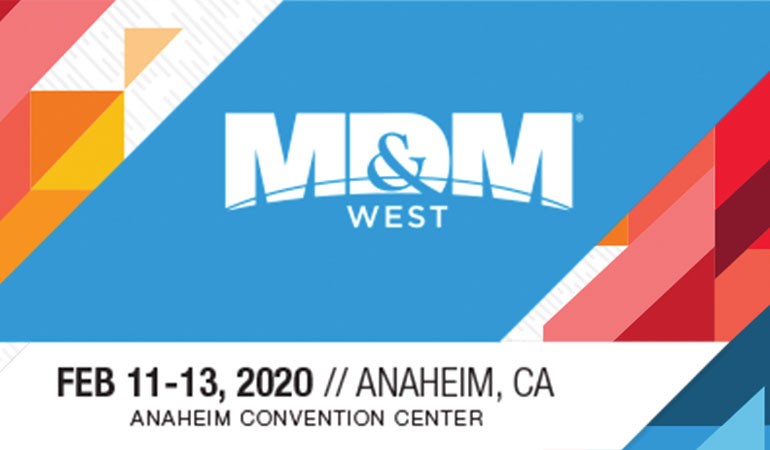
It’s that time of year, again. MD&M – the nation’s largest medical device industry tradeshow – is hosting its West Coast conference in Anaheim, CA, and Ray Products is thrilled to be returning to the floor as an exhibitor. The showcase provides an excellent opportunity for our company to connect with hundreds of engineers, innovators, designers, and large-scale medical device corporations and share the full range of manufacturing solutions our pressure forming and vacuum forming capabilities can provide. We’ve met many of our long-term clients at previous MD&M showcases, and it’s always exciting and inspiring to not only learn of the cutting-edge innovations emerging within the medtech industry but to also be a part of their creation.
Medical devices have always comprised a significant portion of Ray Products’ manufacturing projects. In fact, the plastic product that put our company on the map over 70 years ago was a medical device: one of the earliest clear plastic baby bassinets on the market. Since then, we’ve thermoformed plastic parts and enclosures for countless instruments used in the field of healthcare, including this cancer diagnostic machine, this DNA sequencer, this hospital cart, and many others.
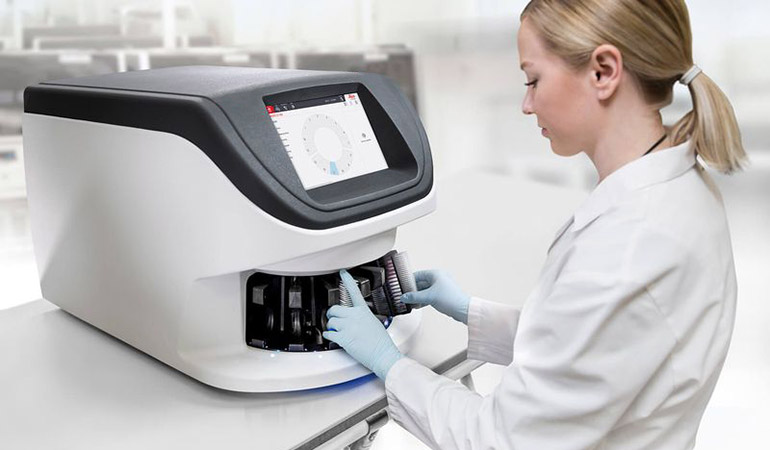
The truth is, we get excited about every plastics manufacturing project that comes into our California-based facility. Still, there are plastic pressure forming projects that stand out for our whole team.
Let us tell you about one of those.
Recently, a leading biotechnology company came to us for help creating the housing of an advanced digital pathology slide scanner.
The project demanded impressive aesthetics, incredible levels of precision, and high-performance materials. In short, it was precisely the type of pressure forming project we love.
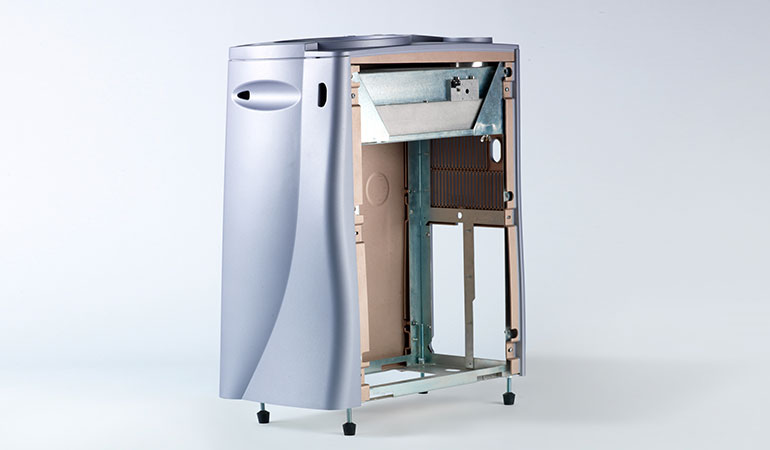
If you pay close attention to manufacturing trends, you may have already seen it happening: manufacturers are discovering the benefits of pressure forming, and realizing that they can’t help but switch.
Why are they switching, and is it the right choice for you?
At Ray Products, we’ve been pressure forming plastic parts for over 70 years, and have a keen sense of the types of projects that can greatly benefit from this process. Below are the most commonly noted reasons to opt for pressure forming for your next project.
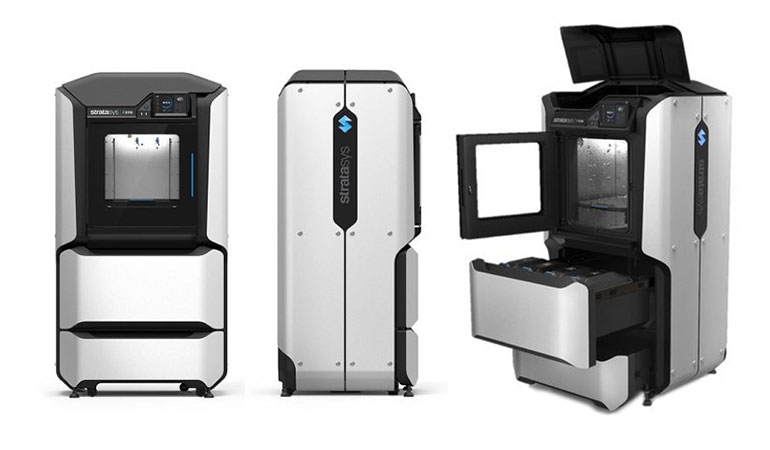
We’re thrilled to announce that Ray Products has been awarded the Gold prize at this year’s SPE Thermoforming Conference for our work on the Stratasys F370 Industrial-grade 3-D printer!
The Society of Plastics Engineers (SPE)’s annual thermoforming conference is the leading exposition where thermoformers, suppliers and clients assemble to attend workshops, discussions, and networking sessions on all things thermoforming. One of the most exciting aspects of the conference is its contest, which considers submissions from thermoformers all over the country across several manufacturing categories.
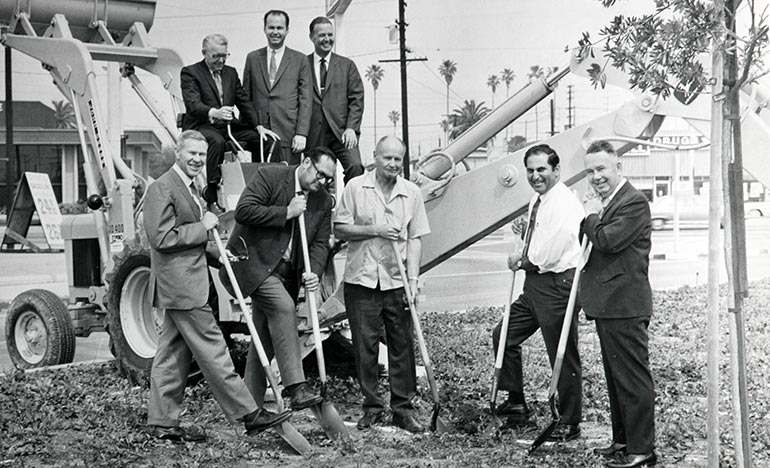
On the last Saturday of March, family, friends, and current and past employees of Ontario-based plastics manufacturer Ray Products gathered at a microbrewery in Upland to celebrate the last 70 years.
Brian Ray, current company President and grandson of the company’s founder, was in attendance with his family, trading memories and jokes with employees and friends at the celebration.
“The average life span of a company is about 15 years,” said Ray. “So I think our 70th anniversary is definitely worth celebrating.”
The company was founded by Allen Ray on April 1, 1949, in a 1,000 sq. ft. shop. Today, Ray Products operates a 48,000 sq. ft. facility in Ontario, CA, equipped with the best available thermoforming technology. The high-quality customized plastic parts that Ray Products produces are used in a wide range of industries, including medical equipment, transportation, green energy, automotive, building and construction, and recreational equipment.
In honor of its 70th, the company commissioned a special bottling named “Loyalty Lager” from Upland microbrewery Last Name Brewing. It was a natural fit, then, to host the anniversary party at the brewery.
On Saturday, some guests swapped stories while enjoying signature sandwiches and burgers from the Big Easy Sandwich food truck. Others enjoyed funny-money gambling tables or took tours of the brewery, while the younger set quite literally bounced off the walls of a bouncy castle.
In between bites, Ray offered his theories on the family-owned manufacturer’s longevity.
“It’s a balance of two things,” said Ray. “On the one hand, we regularly invest millions in the latest advanced thermoforming technology so that we can offer our customers the absolute latest and best. On the other hand, we really value the traditional ways of doing business.”
“We want to do business ‘the right way.’ We respect our customers and partners and the skills of our employees. It’s why our employees stay with us for 10, 20, and sometimes even 50 years.”
In an op-ed he penned last summer, Ray defined three key points of doing business the right way: delivering a quality product, operating as a fair employer and being a reliable partner.
At Saturday’s celebration, the results of that philosophy were clearly visible: hundreds of guests with smiles on their faces, celebrating a company with a 70-year history and no signs of slowing down.
About Ray Products
Ray Products has been manufacturing high-quality 3D thermoformed plastic parts since 1949. Located in Ontario, California, Ray Products uses the most advanced machinery and materials in the business to create custom plastic pieces used in medical equipment, transportation, green energy, automotive, building and construction, recreational equipment, and more.
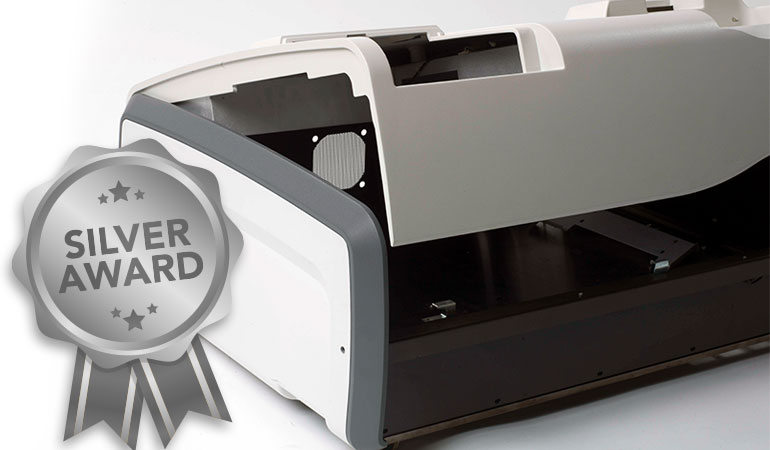
Last month, the Society of Plastics Engineers’ held their annual Thermoforming Conference, where clients, vendors and industry leaders come together for innovative and informative thermoforming workshops and sessions.
One of the best parts of the event is the Parts Competition, which showcases the latest advances in thermoforming design and applications. The best parts receive awards, and we were thrilled to win a silver award this year for a multi-part medical device we made for a client in southern California.
A bit more about the (award-winning, sorry we had to) part:
After developing prototypes that used urethane casting to create the enclosure panels, a medical device manufacturer client was ready to move to mid-scale production. But they quickly realized that the urethane casting process would mean limited manufacturing capacity, high cost per part and could yield issues with consistency from part to part. We had a solution: pressure forming.
By switching from urethane casting to pressure forming, our client was able to significantly lower costs, improve manufacturing speed, increase durability and guarantee part-to-part repeatability while simultaneously planning for future increases in demand and capacity.
We worked closely with the client to reduce the total number of losses, adding in undercut features for rigidity and improved fit, and making other alterations to lower manufacturing and assembly costs and improving aesthetics.
We’re grateful for the recognition (including the shout out in Plastics News) and are gunning for the gold next year!